A glimpse into the future
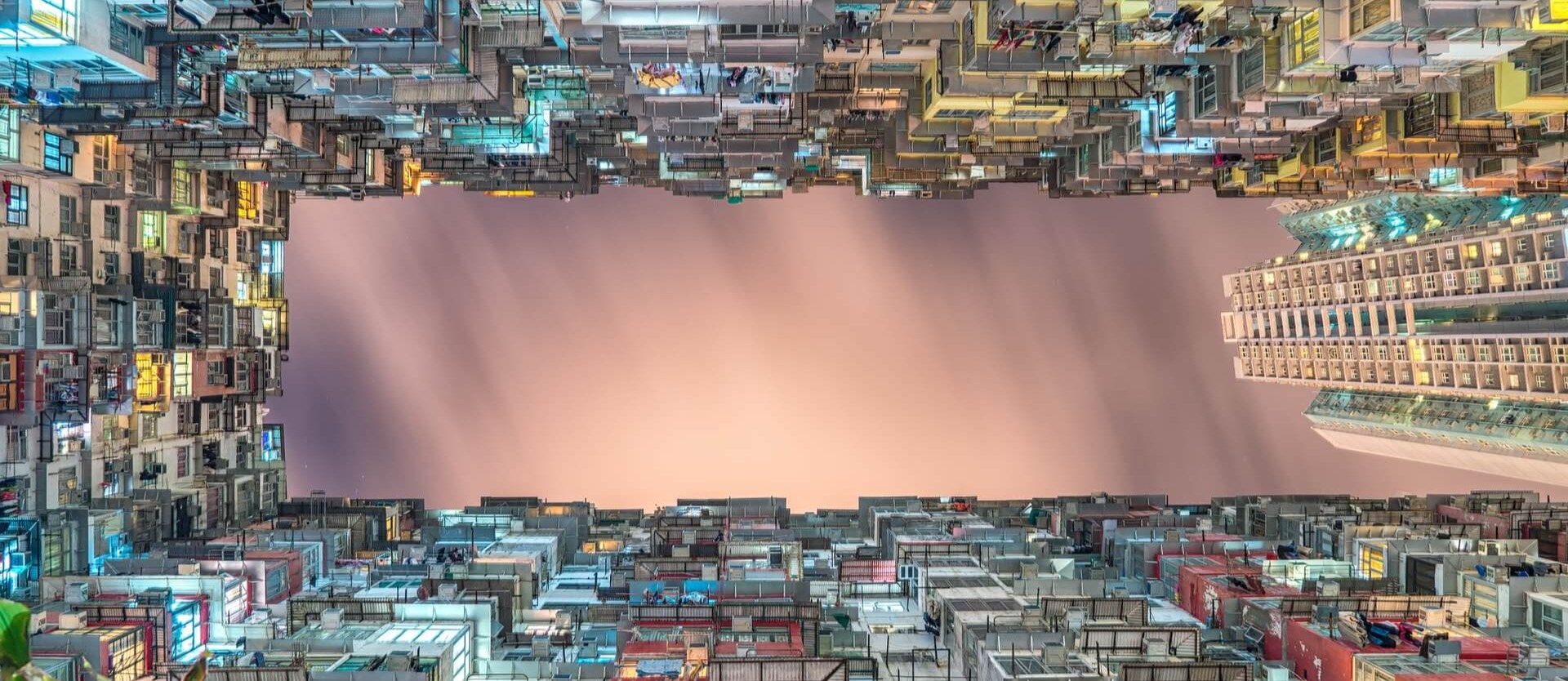
Sustainable production and consumption
More and more people are rapidly moving to the cities – the trend is evident worldwide – even in Sweden. The move to the big city is often motivated by the opportunity for a good education and career. The number of global consumers is increasing, and our lifestyle choices require increasingly advanced products and solutions, while we have realized that resources are limited. That means that it is already a requirement today that production and consumption must be sustainable over time.
Industry 4.0 is already here
Globalization offers room for a broader potential market with more active players. At the same time, competition means that increasingly higher productivity targets are set. In addition, the move to the big city meant that we chose professions outside the industry, making it increasingly challenging to recruit knowledgeable employees needed in a modern industrial company.
To reach these challenging productivity goals and counteract high wage costs and lack of skilled personnel, one must invest in advanced CNC machines and tools, robotic solutions, automated material, and tool handling. In short, all possible forms of automation and IT. Industry 4.0 is already here, and it is estimated that by 2025, 50 billion units in the industry will be connected.
Cutting fluid management needs more attention
When purchasing new cutting equipment, the focus is on productivity, performance, and tolerances for the machining. Cutting fluid management receives little attention because responsibility is unclear and shared between different departments; production, maintenance, purchasing, environment, and the external cutting fluid supplier. With few requirements from the buyer, little technical development has taken place, resulting in operational and maintenance problems and extra costs during production.
The operator's valuable working time is thus spent monitoring and keeping the cutting process going. Today, this often means a modern robot cell with several CNC machines, where automation has been used to minimize deviations and disturbances, including a reduced risk of human influence. With the same machine, the operator must manually measure, note, and then remedy deviations in the quality of the cutting fluid, which no production manager feels works properly.
The cutting fluid is of great significance for the operative result
In the product calculation, the purchase cost of cutting fluid is relatively low, often around 1%, but the actual and total impact on operational performance is often as high as 8-16%. That is because ineffective cutting fluid management leads to:
- Unplanned stops
- Difficulty cleaning
- Work and costs for cutting fluid destruction
- Shorter lifetime of machine and tools
- Excessive consumption of cutting fluid
- Reduced product quality with subsequent costs for measures and lost production time
- Ill health due to high bacteria levels and use of biocides
There is a real challenge and complex set of requirements for the processing industry regarding high productivity requirements, sustainability, an increasingly clear environmental responsibility, a continued lack of personnel, and a constant search to lower costs. There are thus great opportunities to further increase productivity by modernizing the handling of the cutting fluid.
FluidWorker 150 – Automated quality of the cutting fluid
With FluidWorker 150, we at Wallenius Water Innovation have further developed our solutions for industrial UV, which, without using biocides, ensure a sustainable cutting fluid. That is now combined with unique technology for automatic adjustment of the cutting fluid concentration and regulation of the tank level. Thus, processing machines with cutting tools will always have a fully functional cutting fluid with optimal concentration.
The lifespan is extended, resulting in lower costs and reduced water consumption. The FluidWorker 150 is ready for Industry 4.0 with its need for continuous process monitoring and customer requirements in terms of traceability.
FluidWorker 150 takes a big step closer to achieving efficient, safe, and sustainable automation in cutting fluid handling.
Comment