Does the tank level matter?
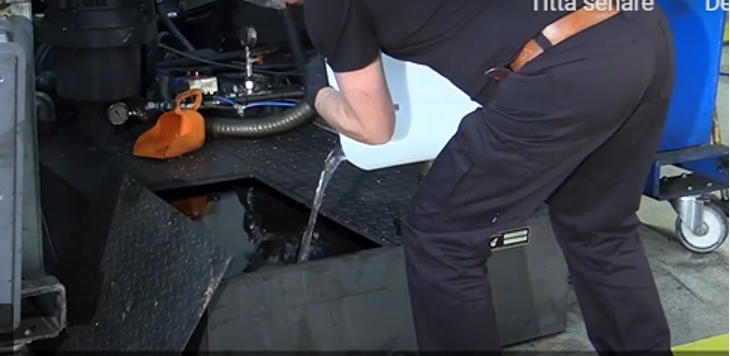
Most people agree that correct concentration in the metalworking fluid is crucial for the production and fluid performance, but many people do not consider the importance of the fluid volume in the same machine tank.
In this blog post, we go through the most common problems that can occur when keeping incorrect volume in the tank.
After more than 10 years in the industry, we have seen many different metalworking fluid systems. Many good and well-designed systems, but also many systems that suffer from various problems - both in terms of design and handling. A common problem is the tank level that often varies over time.
In previous blog posts we have written about the importance of keeping the right concentration,
however, another important area to monitor is the tank volume. By experience, the tank volume can vary a lot, going from almost an empty tank to flooding that creates massive work to clean up around the machine.
Here is what can happen if the volume is incorrect
More dirt in the tank
When the fluid evaporates and is lost via chips and work pieces, the fluid volume decrease. At the same time, the contamination remain, which leads to an increased concentration of particles. This affects the quality of the processed material and enhance the wear on machine and tools. In addition, the risk of foaming grow because small particles can bind the foam and make it more stable. Read more in our blog post about foam. The images below shows how the particle content increases when the same amount of particles are compressed in a smaller volume.
Increased temperature of the cutting fluid
When the fluid volume is lost during processing, the temperature of the fluid will be higher. The cooling properties of the fluid affect the tool's ability to break the chips and a varying temperature will therefore give instable production quality. Many companies purchase cooling systems to keep the temperature of the fluid steady in order to achieve a higher production quality. This involves a cost, both in terms of purchasing the equipment and energy.
How is the level controlled today?
Automatic fill-up systems are becoming more common but is still done manually in most machines. The challenges and risks of manual handling are many and the work is often heavy. Water hoses and barrels with concentrate must be moved to the machine and sometimes the fill-up is made with heavy buckets or containers. When the human factor is part of the process, flooding or incorrect water/concentrate ratio is not unusual. If several machines with different lubrication use the same mixer unit, it is also easy to set the wrong concentration. But, the biggest challenge is probably to refill often enough and to do so before the minimum level has been passed.
So easy but still so difficult
It is in human nature to wait too long before acting on problems, and at that point the limit might have been reached. This point might be when the material is more difficult to process or when the quality is too low.
In advanced machining, it is more likely to solve the problem by investing in cooling and automatic fill-up systems. However, even simpler processing has a lot to gain by better maintenance and the potential savings are normally much greater than we think.
Monitoring and adjustment of the fluid volume has a major impact on the environment and on the profitability. Simple but still quite difficult to manage.
Tips on how to keep the right level
- Visibly mark how large volume the machine tank should be filled with and mark the optimal level clearly.
- Check the fluid daily according to practice and do not forget to check the level in the tank at the same time. Adjust to the right level with the correct mix of concentrate and water.
- Check that the concentration is within the desired range and record the measurement.
Comment